Defibering the future
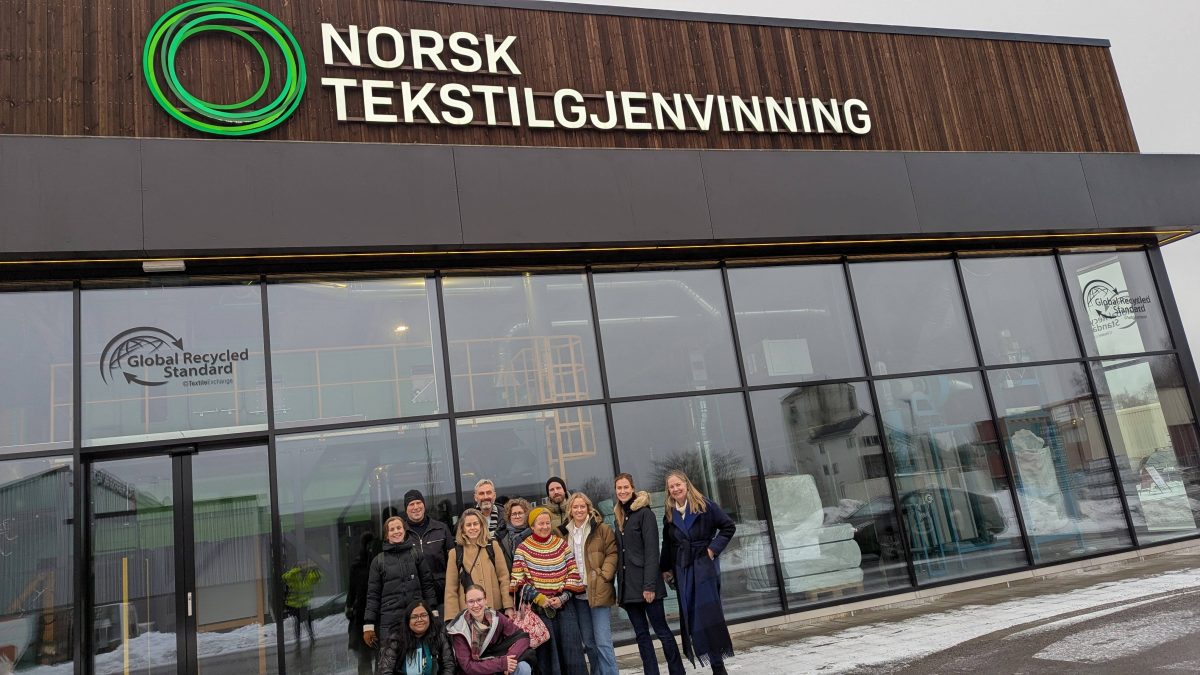
The Wasted Textiles project took the trip to Norsk Tekstilgjenvinning in Sandefjord, and were privy to an introduction to one of the few recycling projects that can actually have something to offer, as the founder Pål Erik Haraldsen has understood the limitations and that it may sometimes be wise to say ‘no’.
Photo, behind, from left: Anita Austigard, IVAR, Bjørn Erik Rui, Vesar, Kristiane Rabben, Mepex, Jens Måge SIRK Norge, Anne-Lene Lundsett, RIG, Ingun Grimstad Klepp, SIFO, Håkon Bratland, SIRKNorge, Alexandra Eng, Revise/NG, journalist, Sofie Nesse Horsberg, Revise/NG. Front row, from left Nazia Nourin Moury og Solveig Birgitte Jacobsen Aarak, both NTNU.
As February started, the SIFO project Wasted Textiles arranged a study tour of the start-up company that has been praised by, among others, the Minister of Environment and Climate as a solution for the future Norsk Tekstilgjenvinning (Norwegian Textilerecovery). Twelve curious men and women from SIFO, Sirk Norge, Mepex, NTNU, Vesar, IVAR, Revise/NG and RIG took the trip and received answers to the many questions they had about this project.
Before a tour of the open and clean factory premises (no reason to take for granted for those of us who have visited recycling companies further south in Europe), we received a clear introduction to the background of NT and the plans for the future. – As of now we sort 1 to 5 tons a day, explained Pål Erik, who started in 2021 – after many years on the supplier side with Healthworkers hospital clothing. Thus, it was the health and hotel sectors that he also started with, because these have uniform products that are easier to work with than textiles from private households.
But what primarily distinguishes this factory from others we have seen, or heard about, is that the fiber to fiber recycling is neither mechanical nor chemical, in the classical sense; it is a ‘defibration’, a more advanced form for mechanical recycling. – I had to come up with a completely new word, explains Pål Erik. The machine, which ‘opens up’ the materials and fibers, is rather unique; the founder found it in Italy and believes it is one of a kind, at least on this scale. Each material that goes into the process, whether it is wool, cotton, polyester or polycotton – requires fine-tuning to obtain fibers that are long enough that they can be carded and spun into new thread and only a small proportion end up being downcycled. Through windows on the machine, we get to see the entire process in practice. Above us, an ingenious humidity system pumps out water vapor, while at the same time the textile dust is sucked out of the air. Should a fire occur, everything stops automatically and is isolated.
Ambitious goals
The latter is incredibly important, because the dust is highly flammable, and when some of us visited a downcycling plant in Poland, we learned – in the smell of foul-smelling anti-mold chemicals – that spontaneous combustion of the textile dust occurred at irregular intervals. That’s just how it was.
During 2025, Pål Erik believes that the plant will have a capacity of 5,000 tons, while long-term plans are for 30,000. To achieve this, automation, AI training and robots are part of the future. In the meantime, the world’s most advanced camera technology is used to identify the fiber content of reference textiles in all mixing ratios. It is the ‘clean’ textiles that can be recycled and defibrated into new thread today, even though they have also experimented with the ‘worst possible mixtures’. – Wool is probably the first thing we will achieve profitability for, he says, showing off the raw material that Gudbrandsdalens Uldvarefabrik will spin from the factory’s own offcuts that previously went to incineration. – We are also working on a project with Aclima, with merino wool.
Economic sustainability and social responsibility are the two most important pillars for NT, sustainability in a more conventional sense he would rather not use about the process, even though it uses both minimal electricity and water – and since they sort by color – no hazardous chemicals. – We have also chosen to say ‘no’ to products from Shein and Temu in our production line, because we do not know enough about the chemicals they use. So, we take these products out.
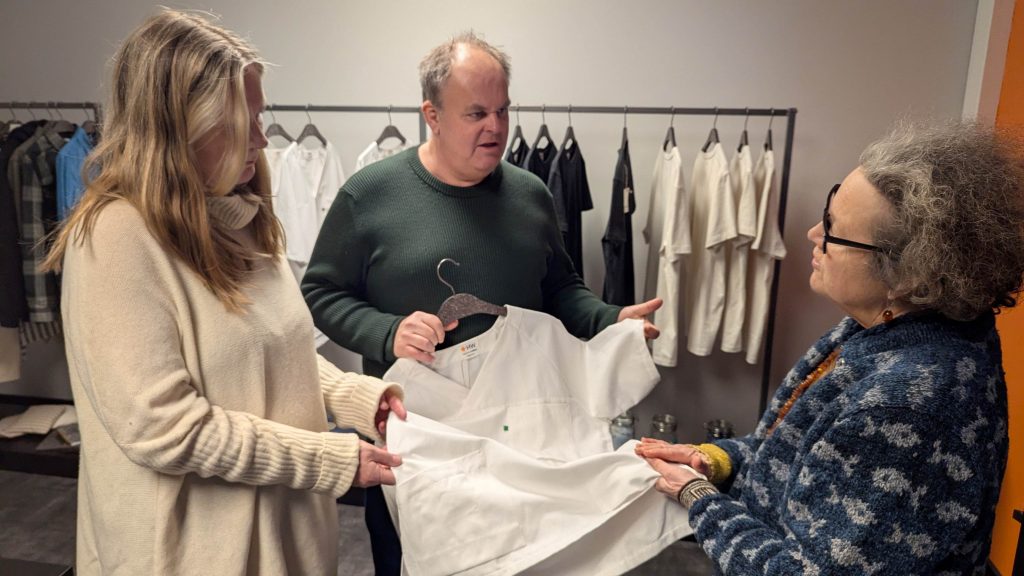
They collaborate with many, including Kirkens Bymisjon and Fretex, who send them what is too damaged to reuse. If they still find things that should be reused rather than shredded, Tise and Finn are the recipients. While we are standing there, a home-knitted polar bear sweater from the 1980s appears. – It is probably acrylic, since it has not been taken out, Pål Erik speculates. We are standing by the machine that takes pictures of all the garments with a hyperspectral “camera”, and based on what it registers and is set to identify, blows the garments out for further processing – today’s do was to sort into cotton, viscose and polyester with a minimum of 95% of this fiber content.
-They must be as clean as possible, in terms of fiber content and of course laundered. We cannot use wet or dirty textiles, and unfortunately the collection towers get damp when they are outdoors. There must be better solutions. For example, collection inside shopping malls. We have also found a solution for 50-50 cotton and polyester.
Because he has hired a Ukrainian textile engineer, he gets good support precisely in finding solutions for the fiber qualities; and when the raw materials, threads or fabrics are tested in the company’s lab, they get a report card that others can be green with envy over. – Maybe we will build a spinning mill here too, as it is not necessarily so labor-intensive.
Not that finding employees is a problem, many people want a job here, we understand. And the prospects for the company – which has received a lot of financial support from Innovation Norway, the Norwegian Retail and Environment Fund and the Research Council, totaling 50 million kroner – are that they could become profitable in 2026. Despite having gone from 50 to 5,000 square meters in no time. But then they charge at ‘both ends’, both from those who want to get rid of the textiles and those who buy the recycled fiber: The cotton is sold to Spain, the wool to Norwegian customers and polycotton also has a market, as mentioned. He also showed off hospital uniforms with 52% recycled fiber, which have withstood both washing and use, and which appear both softer and more comfortable than regular uniforms.
Not a goal to have recycled fiber in everything
They are constantly trying out new solutions, but taking one step at a time. He wants to and believes in trying out hemp as a replacement for polyester in a cotton blend. And otherwise says ‘no’, not only to Shein and Temu, but is also clear that the EU’s idea that all textiles should have recycled content is nonsense. – Curtains are fine with recycled fibers, but fine wool t-shirts, that’s really just nonsense, emphasizes Pål Erik, even though he may be undermining his own business model with such a statement.
He also hopes that there are products that could disappear from use or at least not end up as hostages in the circular economy, as they create major problems. When we ask for a wish list of these, which the Ecodesign for Sustainable Products Regulation could use more ink to get rid of rather than the current focus on physical strength, repairability and recycled content, Pål Erik lists: – Clothes with printed logos, with electronics and sequins, and sportswear with lots of Spandex. He is also not particularly enthusiastic about thin nylon stockings, thongs and bras with underwire – and believes that they belong in residual waste and should be sent to incineration rather than recycling, which is the opposite of what the official policy currently demands. GoreTex jackets, on the other hand, he believes must first and foremost be used ‘up’, and then must be treated as toxic waste and incinerated separately.
Today’s incineration of these does not take into account PFAS, Pål Erik believes. Thus an intermediate storage of such textiles might be necessary until better solutions are found.