VikingGold
VikingGold was a project financed by KreaNord in the autumn of 2013 and lasted until the autumn of 2015. The idea Ingun Grimstad Klepp and Tone Skårdal Tobiasson had as a reaction to the use of Vikings in the marketing of wool (Viking Wool from Norway and Viking Yarns), instead of using quality and tradition – products of low quality and bad taste dominated. The project was led by Gisle Mariani Mardal, Norwegian Fashion Institute, and was a Nordic collaboration. Also included in the project group was Marianne Vedeler from the Museum of Cultural History, University of Oslo. It was the first time KreaNord (the Nordic Council of Ministers) had financed anything related to textiles.
The objective of the project was to present a few but good examples of how it is possible to use knowledge of the Viking’s textiles for beautiful design products. Another important element was to achieve knowledge exchange in the value chain in the Nordic region and to develop products through cooperation between different companies. The idea was to show how an older textile history could be used positively and that the modern textile industry has unused possibilities within local traditions and through providence.
Important for the project was to create meeting points for historical expertise, raw material suppliers and the finished goods industry and designers. These represented people and groups who had not earlier cooperated. Representatives from the industry and designers got access to historical archives and got to see preserved textiles from the Viking Age, alongside knowledge on the Vikings’ clothing and textile production. It was necessary early on to make some choices. Because Marianne Vedeler, the archaeologist in the project, simultaneously was working on a reconstruction of the tunic from Lendebreen, Norway’s oldest garment from around year 300 AD, we chose this as a starting-point. The tunic is about 500 years older than the Viking Age, but diamond twill, which is a weaving-pattern, was widely used in the Viking age. The selected tunic was thoroughly examined and well documented, and this made it possible for us to be able to show both a reconstruction and our industrially produced fabric at the same time. Our collaborators, from sheep farmers to designers, were involved in the decision-making process and the discussions themselves, and were important for enhancing competence and understanding of what compromises must be made when a historical material is to be produced in a modern way.
The wool
We had to choose a breed living in Norway today. The wool in the tunic was not sheared, but ‘pulled’ of the animal in one fleece, when the wool lifted itself naturally and shed in spring. In Norway today, the older breeds do not shed their wool in the same way. For the reconstruction, Old Norwegian sheep (also called wild sheep and the breed that still often sheds) were used, while the VikignGold project used Old Norse (short-tailed) Spæl and Modern (short-tailed) Spæl to get two different shades. Ingvild Espelien took responsibility for the collection of the 200 kilos of wool from two local herds and it was also she who sorted the wool into two shades and cleaned it, and separated some of the coarser guard hairs out of the fleeces.
Spinning
Half of the wool was sent to Hillesvåg Woolen Mill, to spin the weft yarn. Selbu Spinning Mill spun the warp yarn, and both were spun with a z twist, though the warp was a little looser spun. The thickness of the yarn corresponded to 6 nm, as 7 nm was on the border of what the machines could spin. This may appear as a minor detail, however the trade-off between being closest to the original yarn in the tunic, and getting a good raw-material with the wool and the technology we have today, was important. All those involved generously shared their knowledge, alongside learning a lot, not just about the Lendebre discovery and the Viking Age, but also about wool, spinning and weaving today.
Weaving
Ingvild sent the warp yarn first to Krivi Vev, and in order for the yarn in the weft to be as compatible as possible, it was weighed before Hillesvåg started their spinning. No one at Krivi Vev had seen the original fabric, and worked from drawings and pictures in order to set up the pattern and density. A characteristic of older textiles is the lack of symmetry in the patterns. In our eyes, the irregularities appear as faults and not conscious choices. Krivi Vev chose to clean up the pattern a little, and also chose to distribute darker and lighter portions evenly in the weave to counteract clear stripe patterns. The yarn initially seemed more difficult to weave than it actually was. The actual weaving of the 200 meters therefore went quickly and easily.
Click here to watch a video about the weaving process (facebook.com).
Finishing
Krivi Vev has no finishing at Tingvoll, and usually sends their fabrics to Sweden for these types of processes. However, Sjølingstad Woolen Mill museum (which is part of the Vest-Agder museum) assumed responsibility for the last finishing, and although the fabric was a bit too wide, this went well. We chose a very simple and easy finishing, although some of the designers had wanted a felted fabric. For anyone who had seen the fabric before and after treatment, it was striking how much softer and smoother the finished fabric was.
Click here to watch a vide about this (vimeo.com).
Design
Parallel to the actual fabric production, a design competition was announced for a select group of Norwegian and Icelandic designers – and the invited sketches were then exhibited as part of Ta det personlig (Take it personally) exhibition at the Historical Museum in Oslo, where both the Lendebre tunics, the reconstruction and VikingGull were presented. Five Norwegian and two Icelandic designers participated, and among these we picked out three who got several meters of fabric and sewed up the outfits that were shown on the Wool Day in 2015 (Sissel Strand, Connie Riiser Berger and Elisabeth Stray Pedersen). These were also shown at an exhibition at the Coastal Museum in Florø (Tradition and trend: Norwegian wool in all times). In addition, several designers have tried the fabric afterwards: Marianne Mørck (who has used a new textile that Krivi Vev has woven afterwards with ordinary crossbred wool), also Malin Håvarstein and Rebeca Herlung. In addition, Kim Holte has received the material, and both Ingun Klepp and Ingvild Espelien have sewn dresses with the fabric.
The project ended, however parts of it lives on in KRUS, as an example of the use of tradition to produce good, new, Norwegian-produced textiles in wool. The exhibition at Museum of History was opened by (our current Minister of Culture) Trine Skei Grande, who got an introduction to the project by Ingun Grimstad Klepp.
A modern version of the tunica material from the Lende glacier
Wool: 70% Old Norse (short-tailed) Spæl sheep, Class F1S, from Nordfjordeid and Snåsa.
30% Modern white (short-tailed) Spæl sheep, CF1, from Trøndelag, Malvik wool wool station
Classified by Norilia
Color-sorted and removal of some of the coarse cover-wool at Selbu Spinning Mill
Warp: Scoured and spun at Selbu Spinning Mill
Weft: Scoured and spun at Hillesvåg woollen mill
Cloth woven in a diamond twill pattern at Krivi Weaving mill, based on the pattern from the tunic from Lendbreen, however slightly modified for the modern machinery
Post-production work: Sjølingstad Woolen Mill museum
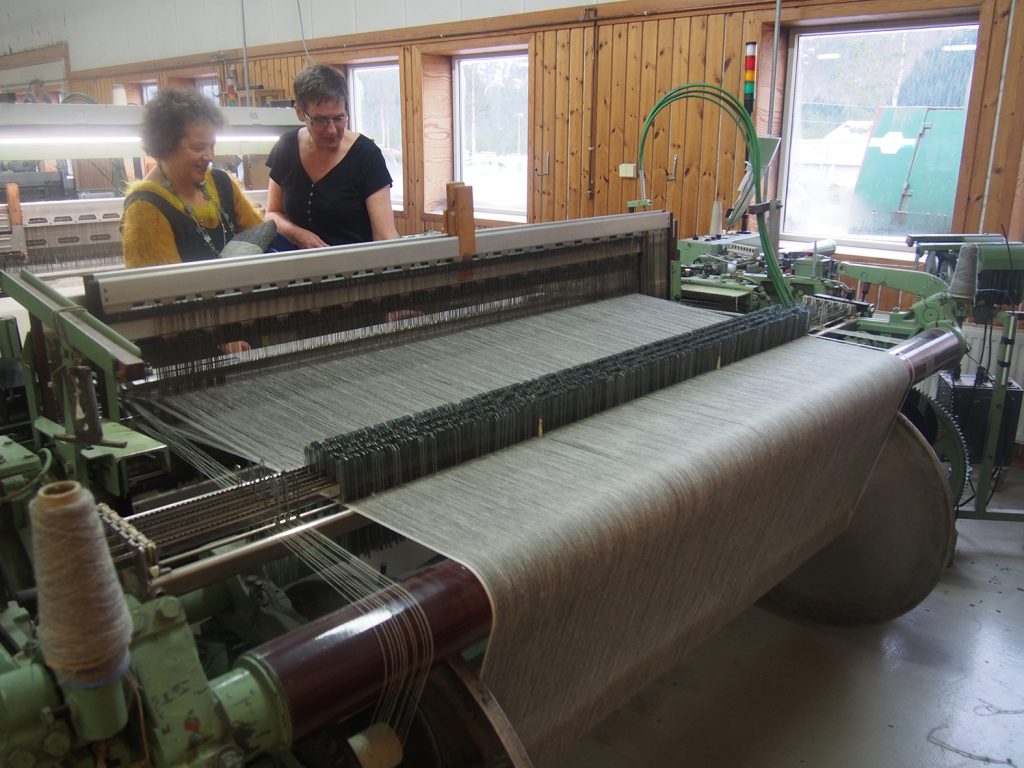
Textile Farmers: Mapping of Fibre and Textile Production in Norway
Summary In this note, we present the results of a survey conducted in the project Textile Farmers and Fashion Agriculture: New momentum for local utilisation of all agricultural resources, led by Fibershed Norway. Based on responses from 124 small and 8 larger entities, we see that the grassroots in the Norwegian textile value chain are…
Continue Reading Textile Farmers: Mapping of Fibre and Textile Production in Norway
How to speak so policymakers listen?
Friday June 27th 2025 Time: 11 -12:30 11th International Degrowth Conference Campus Blindern, Oslo
From Clothes to Skin: Chemical Safety in Ultra-Fast Fashion and Luxury Brands’ Clothes
This literature review explores the presence and associated health risks of hazardous chemicals in clothing, with a particular focus on dermal exposure. It investigates the potential health effects of skin contact with toxic substances in garments and whether clothing sold from fast fashion brands and luxury brands contain different levels of chemicals. It emerged that…
Weigthing Weight: Exploring Clothing Fiber Composition and Its Impact on Garments’ Weight
Author: Rita Dominici Introduction Various textile management policies are under debate, with particular attention to the effectiveness of weight-based eco-modulation, a policy strategy aimed at minimizing the environmental impact of products (Lifset et al., 2023). To better understand this mechanism, it is important to first know that fashion is widely regarded as “one of the least…
The proof ain’t in the pudding
It is common to hear and read about the environmental advantages of longer lasting products, it is everywhere from product advertisement to environmental policy and academic literature. But what is the empirical knowledge substantiating the “durability discourse” across consumer goods? In the recently published literature review in Sustainable Production and Consumption, The environmental impact of…
An Italian gaze on Oslo’s clothing habits
From the eyes of an Italian guest who has just spent her first month in Oslo, I’ve noticed some clear differences in fashion habits and the general relationship people have with clothing here compared to larger Italian cities like Rome, Milan, or Florence. By Rita Dominici What hit me almost immediately, especially during my early…